When a potentially hazardous spill occurs in the workplace—no matter how small—seconds matter. Having a sound spill response plan and communicating that plan companywide is key to protecting life, property, and the environment. And like fire drills, spill response procedures should be practiced frequently, especially if the facility consistently houses hazardous materials. In fact, in the United States, spill response regulations are enforced by OSHA, the EPA, and various state and local agencies.
For larger companies and facilities storing and handling flammable, toxic, or otherwise hazardous liquids or chemicals on a daily basis, those are all obvious points. For smaller businesses who aren’t aware their handful of oil drums or chemical totes may fall under the same regulations, it is important that they find out and have a plan in place.
1. Assess the Risk
The first step during any potentially hazardous leak or spill is to identify the substance or substances, how much has leaked, at what rate it continues to leak, what’s in its path, and just how dangerous the leak or spill actually is or has the potential to become. Remember, invisible toxins released from certain leaks or spills can disperse or become trapped, thereby impacting the actual size of the danger zone.
For large or obviously dangerous leaks or spills that are not safe or manageable by on-site personnel, calling the appropriate authorities and evacuating everyone to a safe location is the first step. For more manageable incidents, there are some key steps to follow.
2. Protect Yourself
If you’re part of the first response team to a hazardous workplace leak or spill that is manageable, you must protect yourself. Wearing the appropriate personal protective equipment based on which substances are involved is crucial. This could be as simple as gloves, goggles, and a rubber apron, or it could be as extreme as a fully encapsulated hazmat suit. If the leak or spill is toxic, the correct respiratory gear will also be needed.
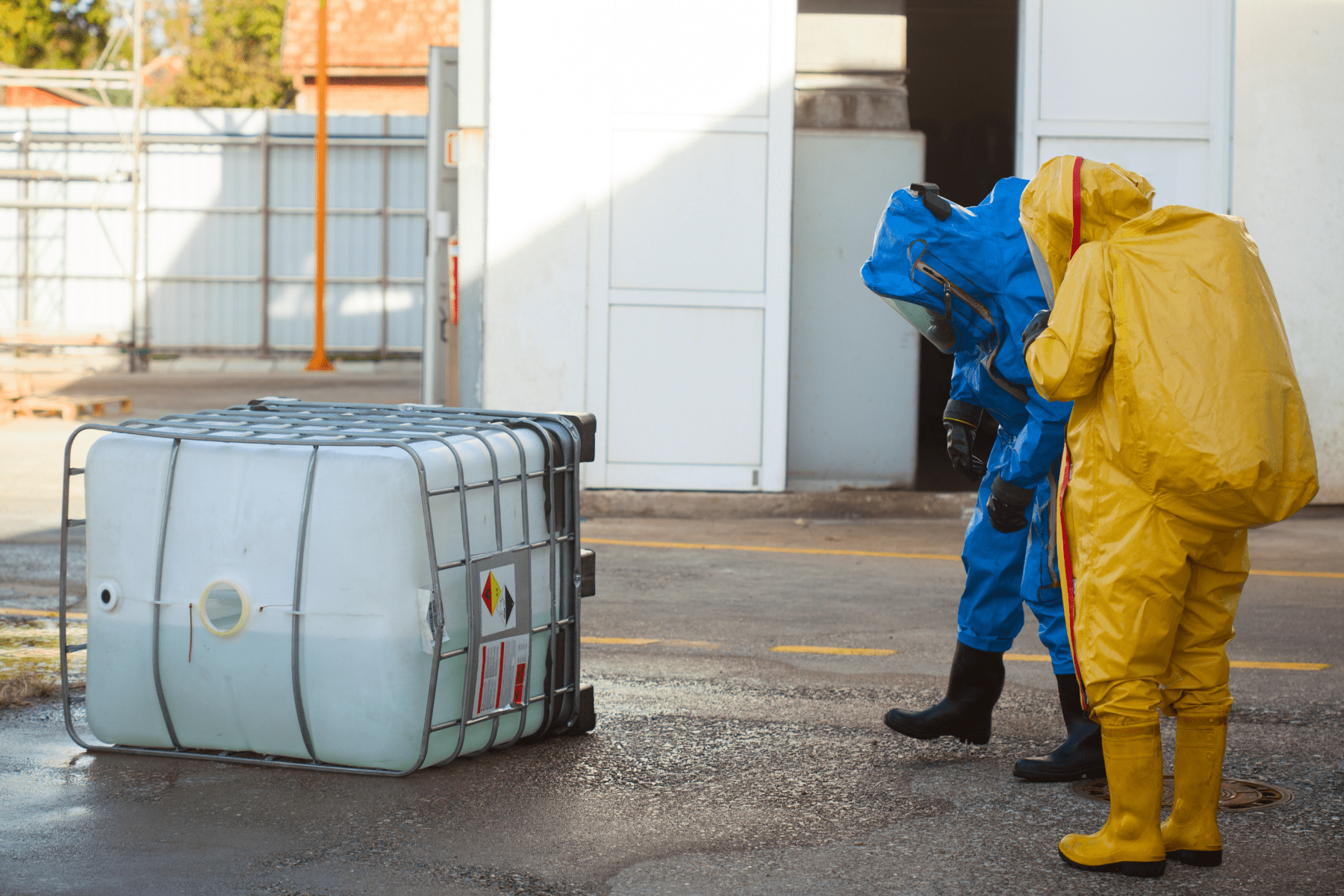
Wearing protective equipment does not equate to immunity. Googles can fall off if not secured properly, gloves and suits can tear due to friction, and breathing apparatuses aren’t always completely airtight if not worn just right. Knowing how to properly wear and move around in protective clothing should be part of every spill response plan and training regiment.
Personal protective equipment must be stored properly and in an area familiar to all personnel who may need to respond to potentially hazardous leaks or spills. This equipment may degrade over time, too, so it’s important to inspect all spill response equipment at least annually.
3. Stop the Leak or Spill
The sooner a workplace hazardous leak or spill can be stopped at its source, the easier it will be to mitigate damage. This could be as easy as rolling or up-righting a drum, engaging a shut-off valve, or sealing a leak with a temporary plug or patch. Just like PPE, keeping things like drum tourniquets, epoxy repair putty, and dowels in your spill kit could change the dynamic of an accidental spill significantly.
A mistake that must be avoided is to stop the leak without wearing the proper PPE. If a 55-gallon drum containing a hazardous liquid were punctured by a forklift, the natural response would be to quickly roll the drum so the breach faces up. Without the proper PPE, however, you risk significant exposure. This is why storing even smaller versions of spill response equipment close by is important. In this example, a small spill kit mounted on the forklift itself would save a significant amount of time.
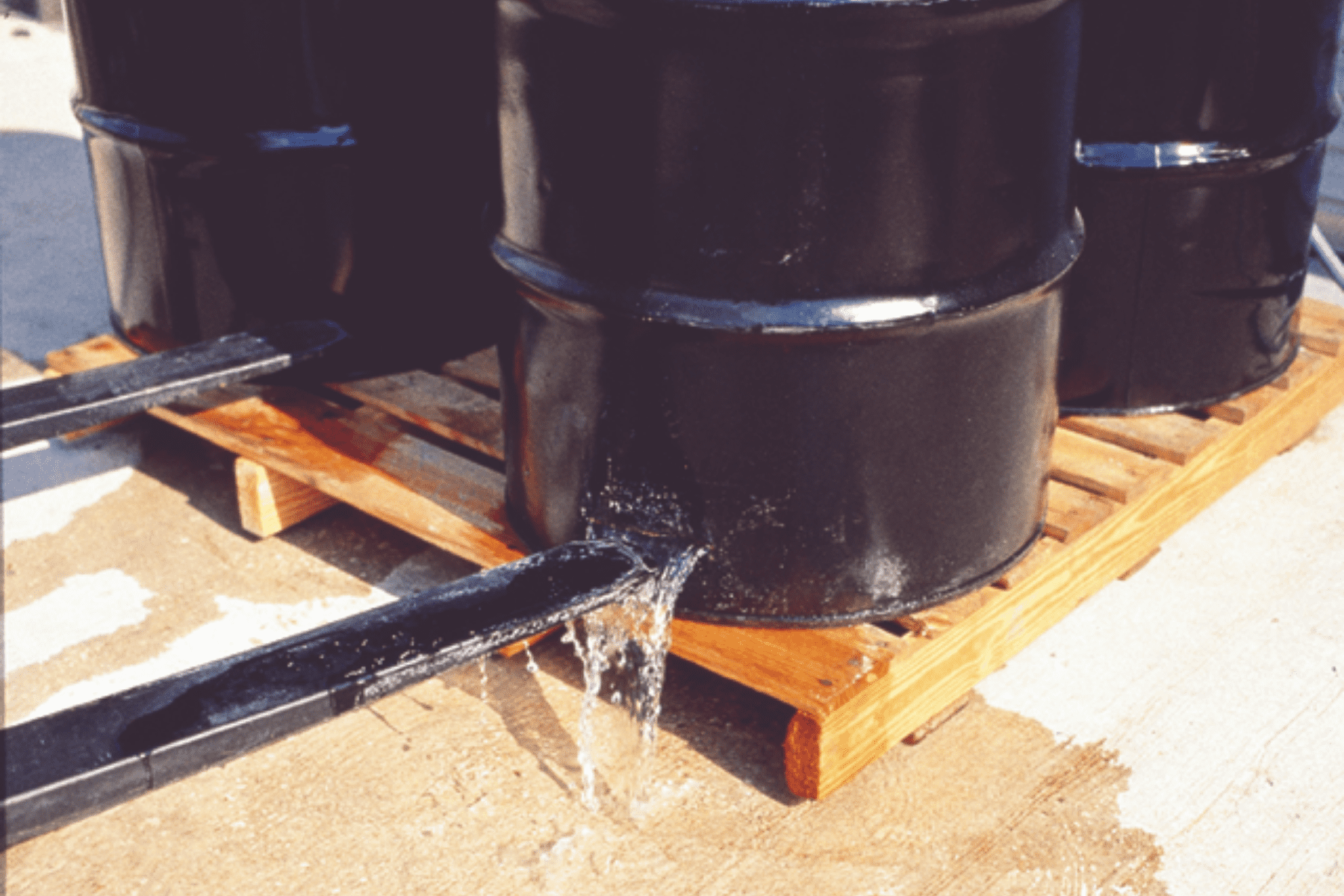
4. Contain the Spill
Stopping the spread of an accidental hazardous materials spill will lessen its impact on the surrounding area. Spill response products such as sorbent socks and even non-absorbent berms will help to keep a dangerous spill under control. When deploying the containment system, you should start at the furthest point of the spill, surrounding it completely so that it becomes fully contained. Be sure to deploy the containment system far enough away from a moving spill so that the liquid doesn’t breach the top of the system, especially if using non-absorbent spill berms or dikes.
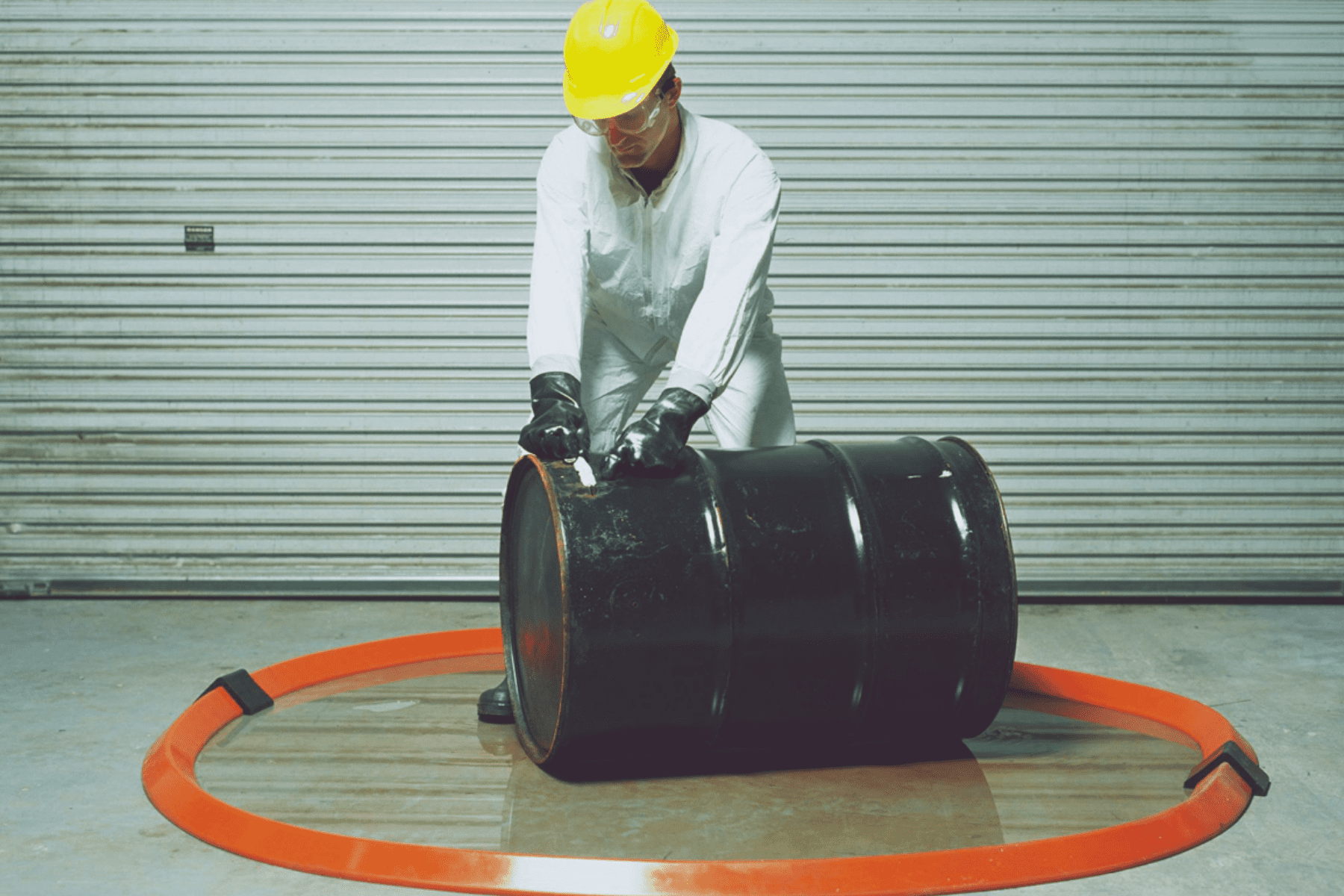
Unlike sorbents, spill berms are easier and more compact to store, faster to deploy, and can be cleaned and used again. Spill berms do not, however, help to clean a spill as most sorbent materials will. Spill berms, like our own Ultra-Spill Berm Plus model, connect to one another, forming a tight seal. Berms like these don’t normally need to be overlapped like sorbent socks, for example. If socks or berms that do not close-connect are not overlapped (which wastes valuable sorbent material and takes up more space) they will likely leak where the socks meet one another to form the barrier.
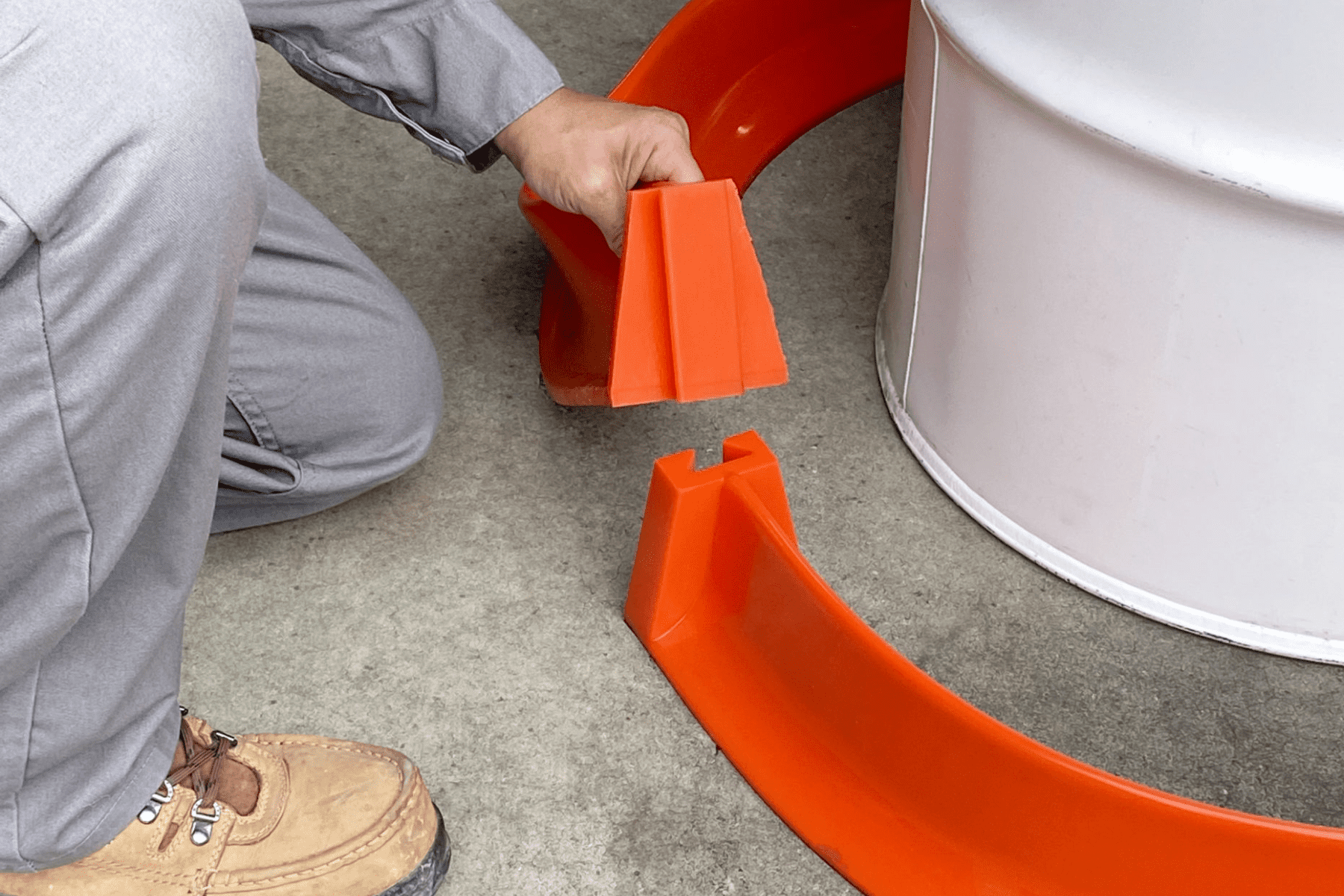
While accidents do happen, having proper secondary spill containment solutions in place will greatly reduce the impact of spills in the first place.
5. Clean the Spill
Cleaning a spill properly depends on what hazardous materials are involved. Sorbents are usually used to absorb the liquid inside the containment area, and then properly disposed of. Sorbents can include specially designed absorbent mats, pads, or pellets. Some liquids can be safely removed using a wet/dry vacuum, pump, or mop. Just be sure you know the best method of clean-up for the type of spill you’re dealing with or you could be creating even more problems.
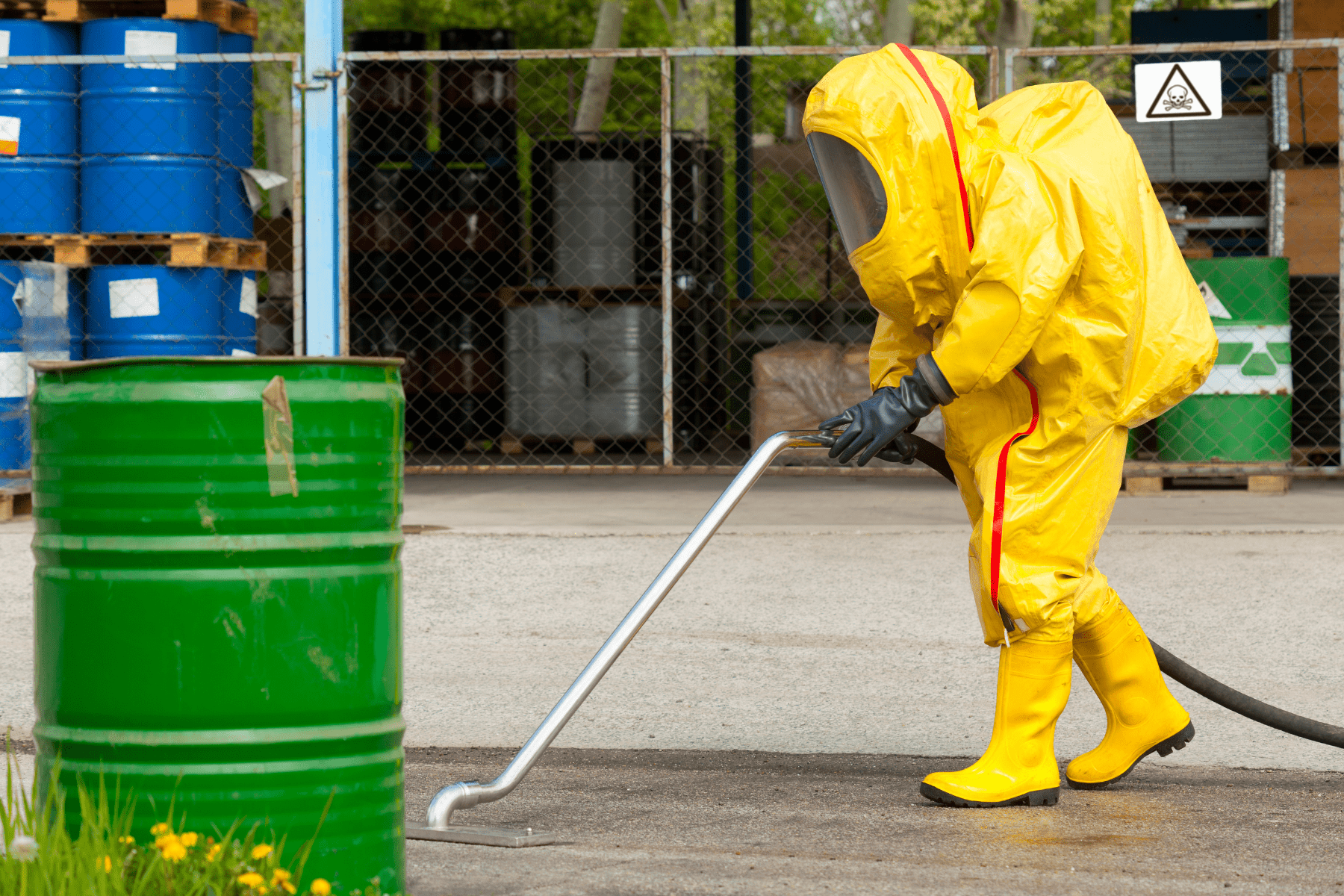
When wearing PPE during clean-up, be aware of how you move around. For example, placing your knee on rough concrete could tear PPE material, exposing you to the spill. Don’t step in and out of the containment area either, as you’ll be tracking potentially dangerous materials outside of that area. And be very certain as to how you are disposing of any sorbents or otherwise recovered liquids. There are regulations and safety concerns to take into account.
6. Decontaminate Personnel & Equipment
After a hazardous spill response (or during, if moving people and equipment in and out of the containment area), it is very important to properly clean all personnel and equipment used during the response. To avoid contaminating anything outside of the containment area, all persons and equipment should be hosed off using the appropriate methods based on what kind of spill was being cleaned.
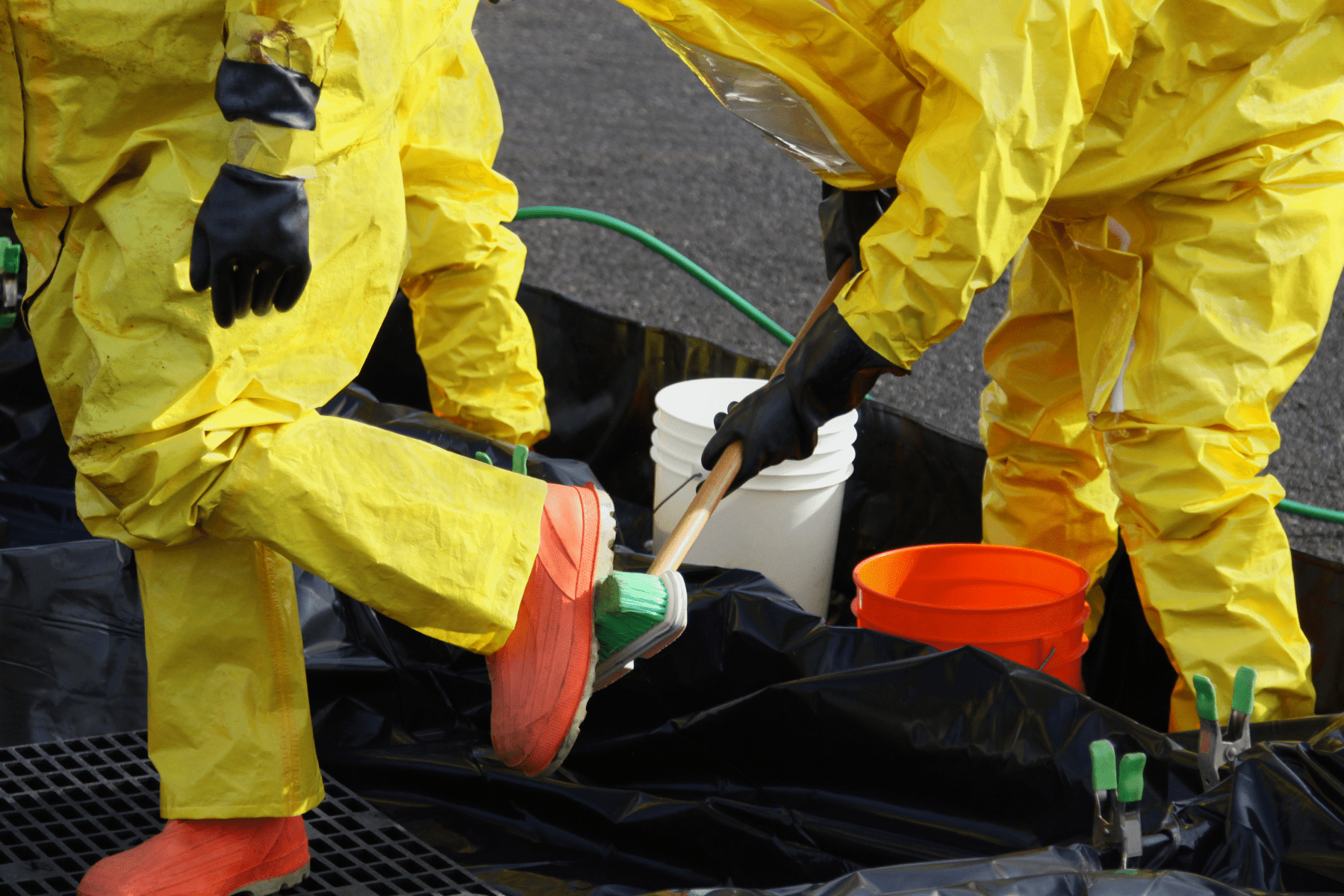
Decontamination (or “decon”) stations should be placed just outside of the hot zone to clean people and equipment coming out. These special stations, like our own Ultra-Decon Deck, are designed to drain and contain the water or other chemicals being used during the decontamination process while keeping people and equipment above the greywater.
Just like the spill cleanup itself, decon equipment and materials must be properly disposed of based on what type of spill occurred.
7. Debrief & Report
After any significant spill response in the workplace, you’ll want to debrief with your team. Your goal is to find out what happened, how it happened, why it happened, and how successful (or not) the response was. With lessons learned, you should revise your spill response plan and training accordingly.
Depending on the type and size of the spill, you may be required to report the spill to local or federal authorities. There are lots of resources online as to who, when, and how to report spills, including resources from the EPA and its various regulatory acts (CERCLA, EPCRA, CWA, TSCA, and RCRA), OSHA, and the DOT. To make any necessary reporting easier, you should always maintain a documented inventory of what hazardous materials are stored on-site, how many, and their location.
8. Replenish Spill Kits & PPE
After a spill response of any size, be sure to replenish your spill kits and personal protective equipment. You should also inspect all equipment that was subject to decontamination, as that process could’ve damaged things like spill berms, vacuums, etc. Carefully inspect all PPE equipment for rips and tears and replace as necessary. Patching PPE is not recommended.
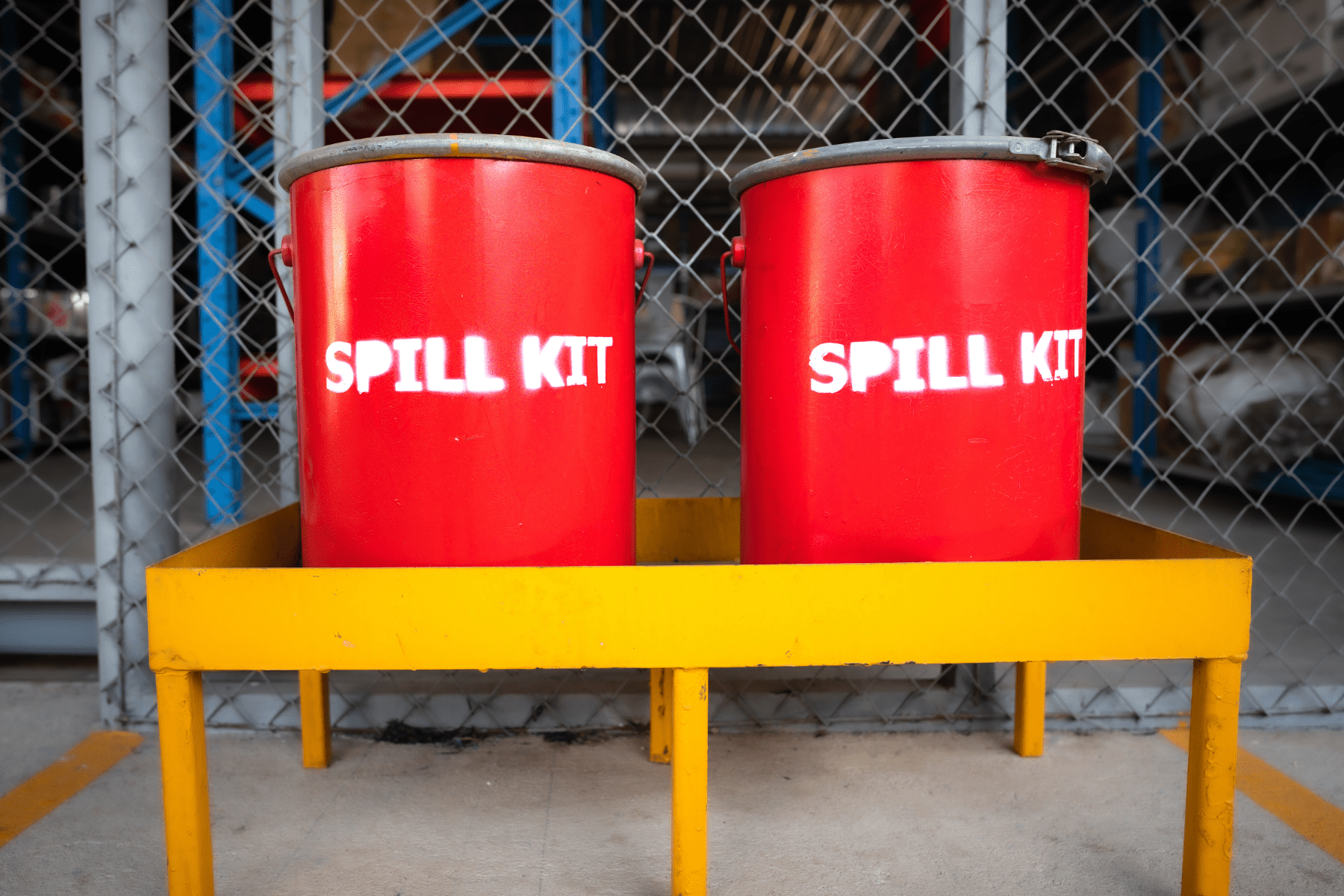